The Ultimate Guide To 3D Printing in Dentistry in 2025
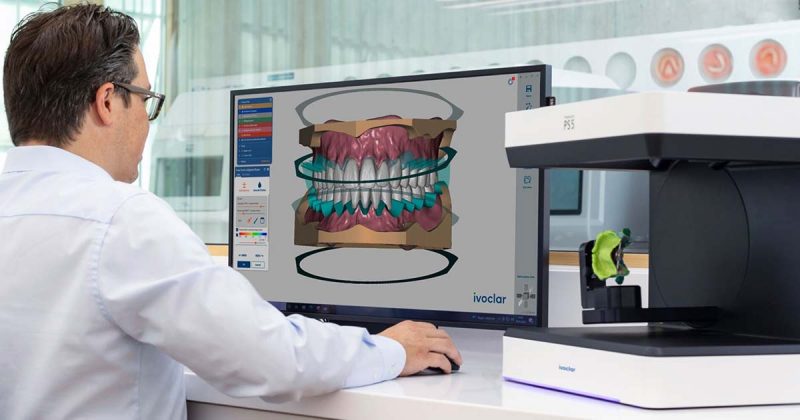
The field of dentistry has always been at the forefront of adopting innovative technologies, and 3D printing is one of the most transformative advancements to date. This cutting-edge technology is revolutionizing how dental professionals approach the design, production, and customization of dental prosthetics.
With 3D printing, dentists can now create highly accurate, patient-specific restorations—such as crowns, bridges, and implants—more efficiently than ever before. This not only enhances precision but also significantly reduces the time spent on production, ultimately improving patient outcomes. In this blog, we will explore the various 3D printing technologies used in dentistry, the materials involved, and the numerous benefits they offer to both practitioners and patients alike.
What is 3D printing?
3D printing also known as additive manufacturing technology is a method of producing three-dimensional products layer-by-layer using computer-aided designing methods. This method reduces material wastage unlike the subtractive method of manufacturing wherein the object is built by cutting away materials from a block until a desired shape and size is achieved.
In dentistry, 3D printing technology has significantly evolved lab work by enabling detailed and precise replication of dental structures while also drastically reducing the time required compared to manual methods.
Different Types of 3D printing technology and process:
Before the 3D printing process begins, digital images of all oral structures are captured using advanced, high-resolution intraoral cameras, and a computer-aided design is then created for the required prosthesis. This data is converted into a specific format that is compatible with 3D printers, which is then used to issue specialized commands for printing. Let us now explore the different technologies through which these commands are executed to achieve the desired results.
1. Material extrusion:
As the name suggests, in this technique the material is extruded from a heated nozzle. The material melted by the heat and extruded gets deposited on the build platform following a pre-programmed, systematic path determined by the software. As the object is formed layer by layer, the platform is lowered continuously with every layer deposition.
This technique can print almost everything and thus has a wide range of applications from prototypes, forms and fit testing, investment casting procedures, jigs, and fixtures to housings and many others since the printing cost is quite low.
Material extrusion technique has subtypes including, Fused Deposition Modeling, 3D bioprinting, and construction 3D printing.
In Dentistry, the Fused Deposition Modeling method of 3D printing is quite often used. Thermoplastic materials present in the form of thin filaments are pushed through a heated nozzle and melted to their melting point. All materials that can be extruded in paste form can use this method of 3D printing to form dental master casts for retention trays, bleaching trays, and more. It can also be used to create temporary crowns and bridges and detailed anatomical study models.
However, materials that require cooling often lead to warping, as seen with zirconia and cast metal frameworks. As a result, while FDM is cost-effective and easy to use, its usage in dentistry is declining as dental professionals increasingly adopt newer technologies that address these drawbacks.

2. Vat Polymerization:
It is a printing technique that creates 3D objects by selectively light-curing photopolymer liquid resin in a vat. Curing is done using light, laser light, or UV light. During this process, the build platform is either lowered into or raised out of a vat of liquid photopolymer resin.
The required object is built by projecting light or a laser onto the platform, which causes the photopolymer to solidify and adhere to the platform. The object is cured layer by layer, and the platform is raised or lowered accordingly as new layers of photopolymer are introduced. Once the 3D object’s layers are cured individually, it is further cured in sunlight or UV light to enhance its mechanical properties. This type of 3D printing has the following subtypes:
- Stereolithography (SLA): This is a popular 3D printing method that uses a light (UV or laser) source to cure liquid resin into a solid form. How does this printer work? The computer generates a design of the required object, which is connected to the 3D printer. This design is converted into a file type known as STL (Standard Tessellation Language) using specific software, which provides geometric data to the 3D printer for generating the object.
The printer contains a mirror, known as a galvanometer or “galvos,” which focuses the beam onto the designated area in a vat full of resin, selectively curing a cross-section in the build area layer by layer. The base layer fuses with subsequent layers, and the build table moves downward. After the completion of the printing process, the object is immersed in another resin and baked under UV light to strengthen the bonding between layers.
This method is widely accepted in resin 3D printing because it produces detailed, highly accurate, and smooth-surfaced objects. However, one disadvantage is that it takes longer to cure a cross-section, as the laser beam focuses on a specified section. This limitation has been overcome by newer methods like Digital Light Processing (DLP), which uses a flash of light to solidify an entire layer of resin simultaneously.
SLA is capable of producing orthodontic aligners, surgical guides, splints, occlusal guards, complete dentures, and temporary and permanent crowns.
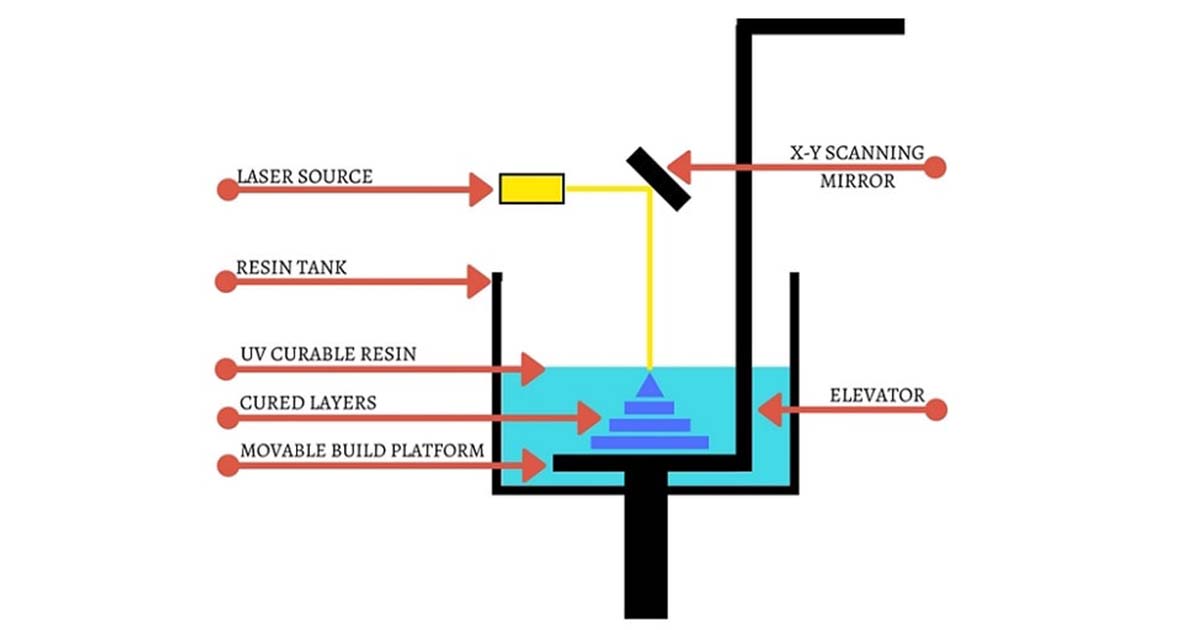
- Digital Light Processing (DLP): A Digital Light Processing printer uses a light projector to flash an image of each layer onto the resin, or several flashes for larger parts, to print an object. It is primarily used for printing larger parts, as the process is faster compared to the SLA method.
The light projector is a digital screen, so the image of each layer is composed of pixels, and the generated layer is formed of small rectangular blocks called voxels. Light is projected using Light-Emitting Diode (LED) screens onto the build platform through a Digital Micromirror Device (DMD). These micromirrors enable the generation of different points of light on the resin at various locations within a single layer, which is then polymerized by the light source. This method is capable of producing high-resolution and smooth-surfaced objects.
The accuracy achieved by these printers allows them to produce partial and complete dentures, thermoform models, surgical guides, aligners, and more.
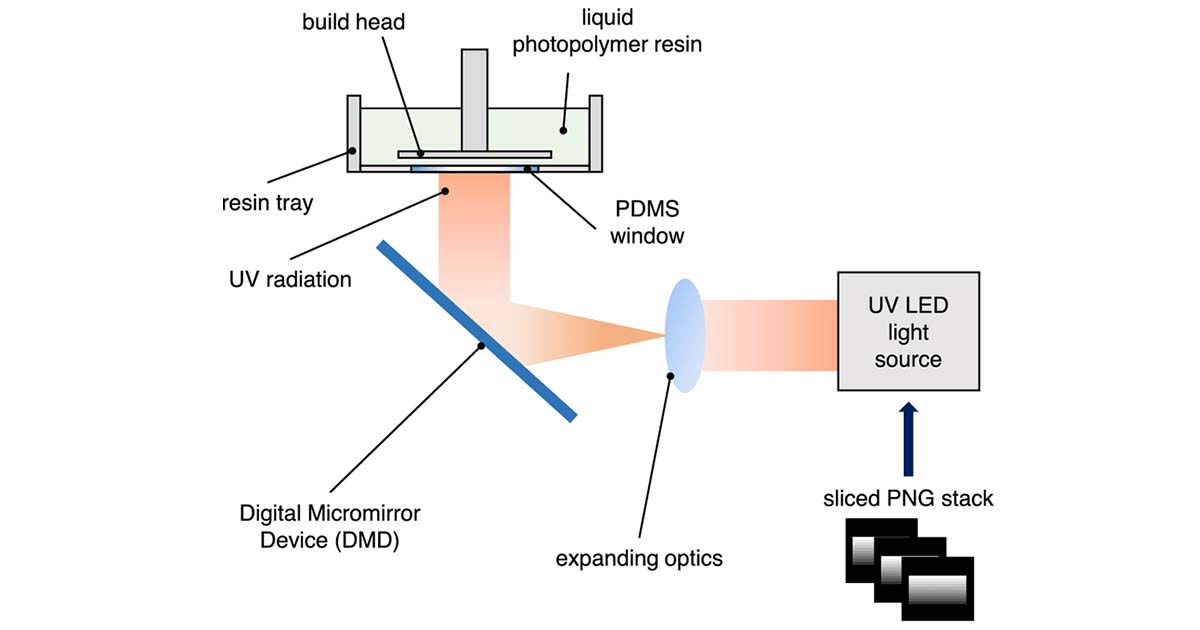
- Masked Stereolithography (mSLA): This printer uses an array of LED light sources rather than a laser or single projection source. Most advanced 3D printers utilize different techniques to filter light to produce the most accurate and detailed objects as commanded by the software. One such technique is Lubricant Photo-curing (LSPc).
This technology combines a UV light array with an LSPc Optical Lens layer for uniformity, which helps optimize the use of an LSPc High Contrast Mask. This mask is responsible for projecting 3D image slices into the vat for layer-by-layer photopolymerization. These printers are capable of the fastest large-volume, high-resolution 3D printing.
mSLA printers produce aligners and retainers, customized braces, surgical guides, precise dentures, and more.

3. Powder Bed Fusion(SLS):
In powder bed fusion, also known as the selective laser sintering technique of 3D printing, powder is used to form an object. It begins with a layer of powder being deposited on the build platform with the help of a roller, followed by CO2 or nitrogen laser beams that fuse the powder into the required shape. The build platform is continuously lowered with each layer being deposited and solidified. One advantage of this method is that it does not require post-processing, and the objects can be finished for color, coating, polishing, etc.
These printers are capable of producing dental components made from metal alloys, ceramics, cermets, etc.
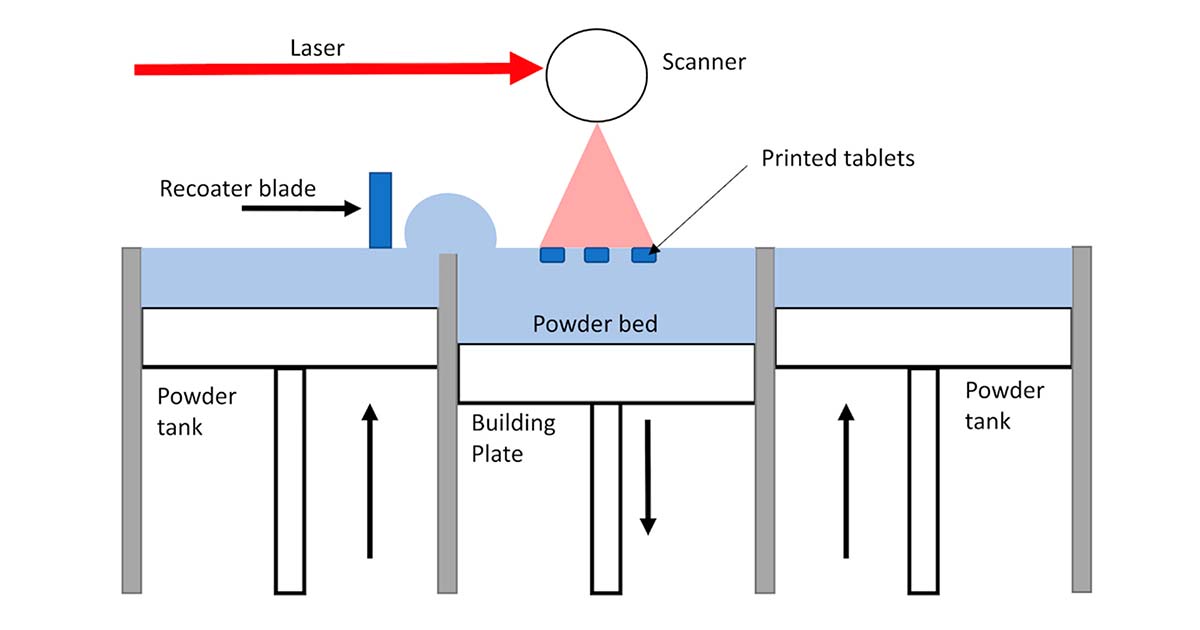
4. Binder Jetting:
This method requires two types of materials: one in powder form and the other in liquid form, which is a bonding agent. This liquid selectively binds regions of a layer of powder. The process requires a coating of the powder layer on the build platform, and a print head moves over this to selectively deposit the binder liquid. The particles thus bonded form the desired shape of the object layer by layer. The object formed is embedded in powder material and needs to be removed. The excess powder can later be reused.
These printers also produce dental components made of metal, ceramics, alloys, etc. Metal frameworks for partial dentures are often produced by these types of printers.
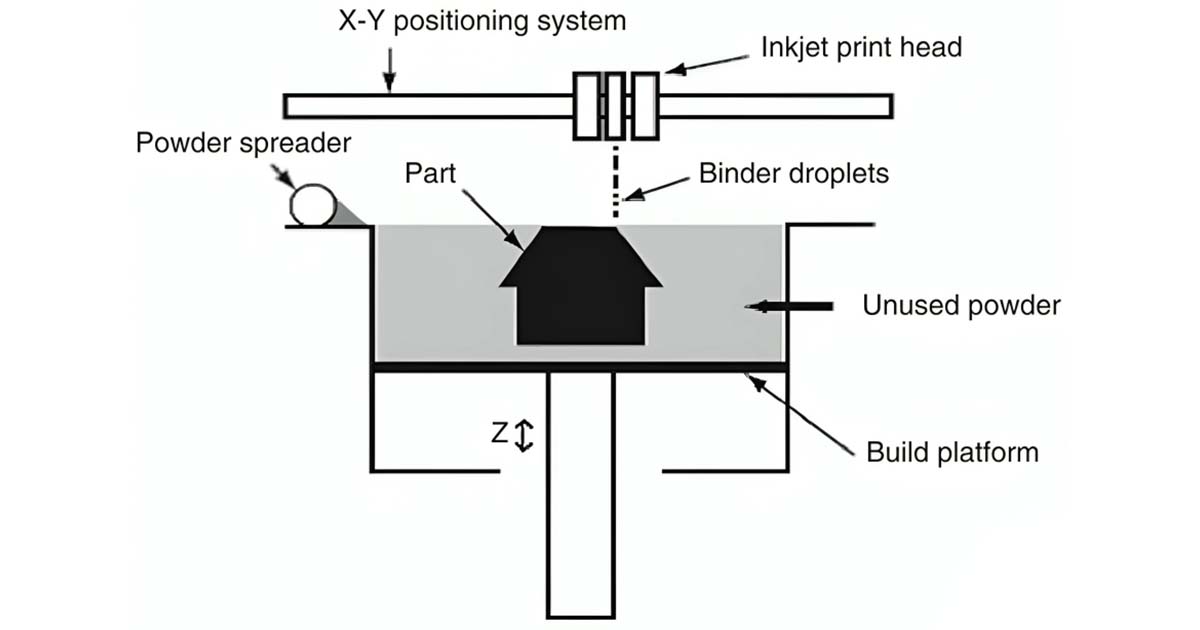
5. Material Jetting:
In this technique, the printhead dispenses photosensitive materials drop by drop onto the build platform, which solidifies under UV light. The objects created in this manner have high dimensional stability and a very smooth finish.
This method is often used to create accurate anatomical models for surgical planning, prosthetics, and dental appliances.

6. Direct Energy Deposition (DED):
Direct energy deposition requires instant powder deposition followed by a laser beam for its fusion. It is used for metals only and is not very popular in the dental field due to the diversity of materials used in other printing technologies.
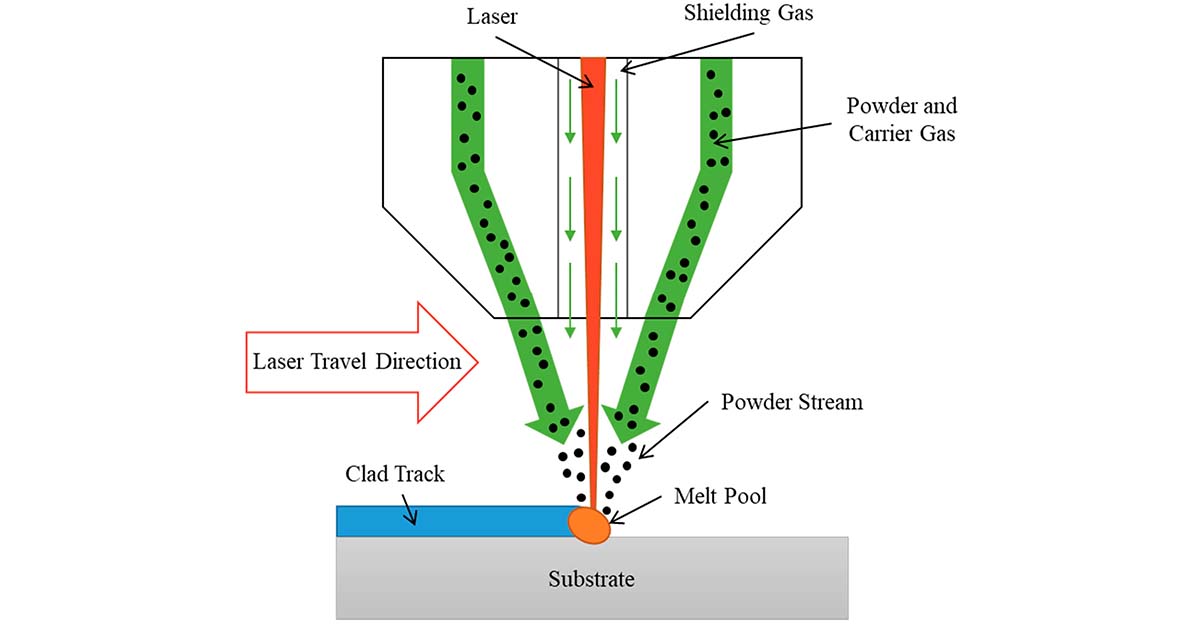
7. Sheet Lamination:
This is a 3D printing method that requires stacking and bonding very thin sheets to one another, followed by cutting them mechanically or through laser into the desired shape. It is often not preferred by dentists due to its limited applications.
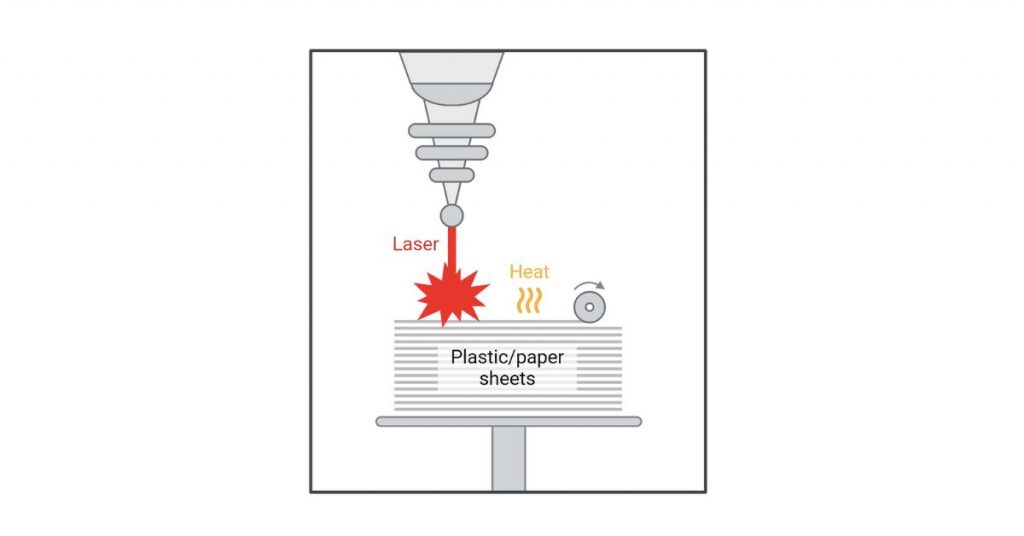
3D Printing Materials Used in Dentistry:
Different applications in dentistry require different 3D printing techniques using various types of dental materials in daily dental practice. But what are these 3D printing materials? Let us break them down for you.
1. Polymers:
Polymers are the most widely used materials for replicating structures into cast models or for manufacturing surgical guides, impression trays, temporary crowns, etc. Resin types like polymethyl methacrylate (PMMA), polylactic acid (PLA), polycaprolactone (PCA), poly lactic-co-glycolic acid (PGLA), and ultraviolet (UV) resins are commonly used in routine printing procedures. These materials are mostly used in FDM-type 3D printers but can also be used with other resin-compatible printers.
- PCA: It is an aliphatic polyester with superior biocompatibility and is widely used in the biomedical field. PCA and its composites are used in tissue engineering, such as membranes for guided bone regeneration. A mixture containing bioactive materials, such as hydroxyapatite, β-tricalcium phosphate, and rhBMP-2, enhances biocompatibility and promotes new bone formation in in vivo experiments.
- PMMA: It is the most commonly used, low-cost, easy-to-manufacture resin in dentistry. It is used for making temporary crowns and bridges, obturators, orthodontic retainers, denture bases, etc. It can also be used in SLA-type printers, in addition to FDM.
- PLA: It is also an aliphatic polyester and hydrophilic. PLA can also be used for forming hybrid materials for guided bone regeneration and biological scaffolds. Apart from this, it can be printed to form surgical implant guides.
- PGLA: It is a copolymer, biodegradable, and biocompatible material. This material is also used for the formation of biological membranes.
- UV Resin: It has high curing efficiency, low energy consumption, and low cost. It is majorly used in retainers, complete and partial dentures, surgical guides, etc.
2. Metals:
Metals have ideal mechanical and biological properties, but their aesthetics and higher cost render them less than optimal for use. Commonly used metals are titanium alloys and Co-Cr alloys.
- Ti and its alloys: They can be used in SLS and other modified technology printers. This metal has an extremely stable chemical oxide film, excellent mechanical properties, and biocompatibility, but also has poor wear resistance, high cost, and potential toxicity. It is commonly used as dental implants and scaffolds, dental crowns, and denture frameworks when 3D printed.
- Co-Cr: It can also be used in SLS and other modified technology printers. Co-Cr has excellent mechanical properties, corrosion resistance, and good porcelain bonding properties. However, it can also cause potential allergic reactions. It is used to print RPD frameworks, FPD frameworks, crowns, and cast post-and-core.
- Stainless Steel: It has superior physical properties, biocompatibility, excellent bactericidal ability, but low mechanical properties. It is mainly used for printing implants and orthodontic components.
3. Ceramics:
Ceramics have become ideal materials for dental restorations because of their excellent mechanical properties, biocompatibility, good abrasion and corrosion resistance, and esthetic characteristics, similar to natural teeth. The most commonly used ceramic types in 3D printing are glass, zirconia, and alumina ceramics. These are primarily printed using SLS-type 3D printing technology, except for alumina, which can also be used in FDM.
- Glass: This type of ceramic has high mechanical strength, low electrical conductivity, a high dielectric constant, good mechanical processing properties, chemical resistance, and thermal stability. It is used in implant coatings and bone regeneration in periodontal treatment.
- Zirconia: Zirconia is biocompatible, osteoconductive, has high strength, and reduced inflammatory response. However, it also has high internal stress, is prone to cracking after sintering, and has high-volume shrinkage. It is mainly used in 3D-printed crowns and bridge restorations, and implant abutments.
- Alumina: This ceramic has high mechanical strength, excellent chemical stability, and good electrical insulation properties but is prone to fracture. It is commonly 3D printed for implants, crowns, bridges, veneers, orthodontic brackets, dental composites, and bone cement materials.
Why 3D printers would take over the traditional labs?
The integration of 3D printing technology has transformed the manufacturing of dental restorations, dentures, and appliances. Patient-specific customizations can now be achieved with greater accuracy and in less time, reducing procedure durations while providing durable and high-quality dental prostheses. Modern 3D printers significantly minimize material wastage by directly printing devices like mouthguards, splints, aligners, and retainers. Their compact size reduces reliance on traditional labs, enabling dentists to use these machines in their clinics, thereby eliminating the need for shipping impressions and materials to labs.
Additionally, 3D printing reduces the number of patient appointments required for accurate fittings, often cutting them down to just one or two. A single machine can produce a variety of dental products by simply swapping materials, enhancing efficiency and versatility. This innovation not only streamlines workflows for dental professionals but also delivers faster and more convenient solutions for patients, making 3D printers a strong contender to replace traditional dental labs.
Conclusion:
This guide has provided an in-depth look at the various 3D printing technologies used in dentistry, from material extrusion and vat polymerization to powder bed fusion and more. Each method offers unique advantages, allowing dental professionals to select the most suitable one based on their needs and preferences. With this knowledge, you can confidently explore the 3D printing options that best align with your practice’s goals.
To explore 3D printing solutions for your dental practice, DentalKart offers a wide range of advanced 3D printers and materials tailored to your needs. Whether you’re looking to enhance your workflow or create custom restorations, DentalKart has everything you need to step into the future of dentistry.
No Comment